

They worked on a mounting frame so they can quickly add and test prototypes as well as attach an array of sensors. This year, the team tested how a small drive base behaves in comparison to drive bases from past years. This is a pneumatic powered catapult that is designed to have a versatile and robust design that can be easily integrated onto a robot. It utilizes new manufacturing and assembly techniques. The goal of this year’s cascade is to iterate upon and perfect the cascade elevator the team started a few years back. This system is designed to funnel a hopper full of whiffle balls into a single flywheel that is mounted on a “Lazy Susan.” The team designed it using a “touch it own it” mindset, and also wanted the design to only utilize motors. The Rotary Intake is designed to intake Stronghold Boulders and retract within the frame perimeter by rotating. This was based on the lessons the team learned from MULE 3. This offseason, the team incorporated a new feature that allows them to pass commands through the path planner, transforming it into an auto builder.Ĭonfigurable drivebase using the SolidWorks equation manager and configurations. The path planner helps us create our autonomous. It utilizes two pneumatic pistons to actuate the grabbers. This claw is designed to pick up the 13 by 13 by 11 in blocks from 2018 FIRST Power Up. This is a fast turning, pulley-driven turret It will also require spring tension to keep the intake plates close together until the driver actually intakes the Power Cube, and most of it will be manufactured using the CNC. This is an intake that is made to pick up the 2018 FIRST Power Up cube with 2 775pro motors on each side rotating the compliant wheels.
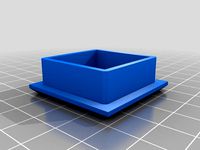
This design aims to prevent back drive and other complications as seen with subsystems like the ratchet. This is a worm gear winch used to power a cascade.
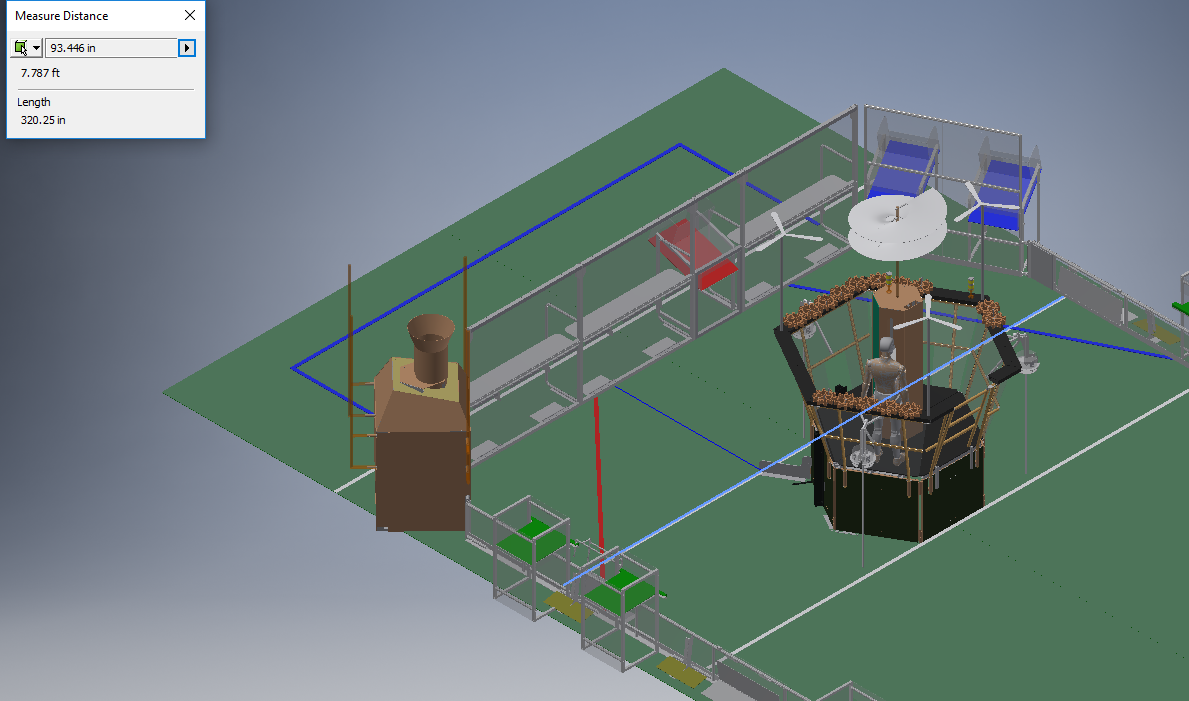
The current plastic is Delrin, and it works pretty well, but you need a bit of tolerance between the metal and Delrin for best sliding.
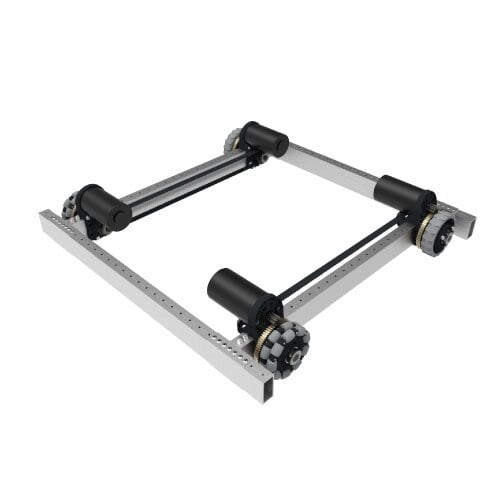
It is chain-driven with stringing taking over for the later stages. This cascade was designed to replace the bearing structure with slippery plastic plates. This is a center-drop drive base with equation-driven dimensions and gearbox. It can be 3d printed or can be modified to be cut on a CNC machine, laser printer, etc. In addition to the encoder, this also requires a rotary spring and a tape for a full assembly. This mechanism allows us to measure linear motion with a rotary encoder attached to a length of tape. Our team GitHub, which contains all the code we've written in previous years, as well as many off-season projects we have worked on in the past.
